BRAUM’S ICE CREAM GETS SWEETER WITH MOBILE APPS
Braum’s Ice Cream and Dairy Stores operates one of the largest dairy farms in the world. The 10,000-acre family farm is home to Braum’s private dairy herd, milk barn, processing plant, bakery and warehouse distribution facility, truck maintenance and water treatment plant. Milk from the dairy is used to make its deliciously popular ice cream, bottled milk, yogurt, cottage cheese and more. Products are then delivered to over 280 Braum’s stores across Oklahoma, Texas, Missouri, Arkansas and Kansas.
The Challenge
Ten area managers and 40 district managers are responsible for overseeing day-to-day operations and growth of Braum’s stores – all which include a grill, an old-fashioned ice cream fountain and Fresh Market groceries. Managers work together to provide a satisfying customer experience while overseeing store personnel, inspections, inventory and importantly, meeting sales goals. However, the only way managers could access back-office administrative and sales performance reports were from a PC in a store or at the corporate office. While productive, managers were confined to a desk.
In addition, Braum’s maintenance inventory management processes required maintenance workers to manually record parts usage, transfers, purchases and physical inventory of their work truck on a piece of paper. At the end of the month, workers would submit their reports to corporate where the data entry team would key information into their system. The process was slow, prone to error and only after the reports were compiled, would the maintenance department then have insight into available inventory. Oftentimes, workers would have to drive from one Braum’s warehouse to the next, or make additional stops at big box stores to replenish their stock – reducing the time they have to make critical repairs.
Paul Clark, Braum’s CIO, knew a mobile solution would deliver the real-time information managers needed in the field and improve the maintenance department’s operational processes.
The Solution
After careful research, Clark selected the LANSA platform for application development and building native mobile apps. Clark decided the cohesion between the capabilities of LANSA and his lean team’s skill sets, and the ability to seamlessly integrate with their existing environment was the best fit for the company’s present and ongoing mobile development needs. Clark started a 30-day trial and asked his senior programmer to give it a test drive.
“I had no mobile app development experience prior to this trial,” said Ezra Daniels, Braum’s senior programmer. “Through the templates and examples in the LANSA platform, a detailed user guide and a few support calls, I was able to quickly learn. It did not take me long to build our first app.”
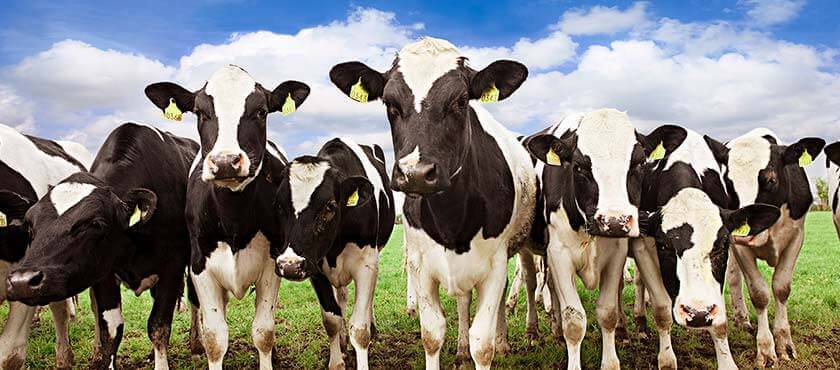
The Benefits
Together, Clark and Daniels worked with Braum’s VP of sales, who oversees the district and area managers who all carry company iPhones and iPads. Daniels’ first project was to replace a paper-based customer feedback/complaint system with an iOS mobile app. (Note that the LANSA platform supports iOS, Android and other mobile platforms.) As a result, managers no longer have to wait for a nightly report to respond to customer inquiries. They receive a notification via the mobile app and can resolve issues and inquires with customers right away.
“Once this application was rolled out, it wasn’t long before we were able to fully use all of LANSA’s capability for our company. Business reports that were once only accessible through back-office PCs quickly became available on mobile phones and tablets,” said Daniels.
Daniels estimates that 90 percent of what the district and area managers’ apps do is extend reporting and knowledge-based information to the managers such as inventory, sales, speed of service results, store inspections, staffing goals, employee history, work schedules, store specific pictures and much more.
“All of these line-of-business reports existed before, but were buried. Our managers were slaves to the back- office PC. If they weren’t in front of a computer they weren’t getting the information they needed,” said Daniels.
LANSA was such a success for its district and area managers, Braum’s decided to create an entirely new system for its maintenance workers as well.
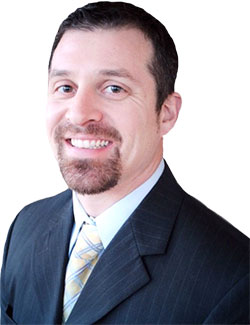
The company’s maintenance department services its stores when issues with grills, refrigerators, repairs and replacements arise and is responsible for recording parts usage, purchases and inventory of their truck. Daniels helped completely revamp the maintenance system, whereby enabling all inventory measures to be recorded in a mobile app. Because all transfers and purchases are recorded in their LANSA applications, Braum’s inventory management system will automatically replenish workers trucks with parts based on their usage.
“They can see real-time inventory of their trucks or other workers trucks so can make transfers quickly. There is no more data entry at the end of the month to record past transactions and even more important, we have eliminated three expensive regional warehouses. Now, we have one central location to more easily keep stock and store inventory.”
Approximately 40 maintenance workers access apps on both iPad and Android tablets. Daniels expressed appreciation for LANSA’s cross- platform capabilities, saying it doesn’t matter what platform their apps are built on, they flow well from iOS to Android.
“A computer programmer takes pride in his or her work like any other profession, but many times there is not that tangible end result you showcase, such as a landscaper or a mason after a completed project. It is extremely gratifying to see a mobile app in production that looks professional, works well, and is a huge asset for your company. I have gotten more “thank yous” from developing mobile apps using LANSA for the past couple of years than I have gotten in the past 20 years of developing workstation programs and desktop apps.”
Once this application was rolled out, it wasn’t long before we were able to fully use all of LANSA’s capability for our company. Business reports that were once only accessible through back-office PCs quickly became available on mobile phones and tablets.
Company and System Information

- Braum’s Ice Cream and Dairy Stores is one of the largest dairy operations in the world. The heart of the company’s operations is the 10,000 acre family farm located in Tuttle, Oklahoma. The farm is home to Braum’s private dairy herd, milk barn, processing plant, bakery and warehouse distribution facility, truck maintenance facility and water treatment plant. Braum’s proudly operates 280 stores across Oklahoma, Texas, Missouri, Arkansas and Kansas.
- For more information visit: www.braums.com