KAWASAKI ASSEMBLY STAFF GOES MOBILE
Kawasaki Motors Manufacturing Corp., U.S.A.’s consumer products division in Lincoln, Nebraska, has replaced its
card-based Kanban system with an electronic solution. The new eKanban solution was developed by KMM’s in-house development team with the LANSA tool set and integrates with KMM’s IBM i and LANSA-based ERP system. Assembly and warehouse staff access then solution from iPads with native mobile apps developed with LongRange from LANSA, a mobile app toolkit for IBM i developers. Staff on the floor also use the mobile apps for cycle counting, scrap reporting, recording of inventory location moves and other warehouse and assembly related tasks.
“The solution is saving over US$3,500 per day and we expect very quick ROI. What we have done today is just the beginning. Our developers are very experienced enhancing the functionality of our ERP system, which was the largest part of this project. Initially we didn’t think we had the skills to develop the native mobile apps ourselves, as LongRange only became available towards the end of our project. The mobile apps were developed by 3 of our IBM i developers. We launched our first series of apps in just 2 months, from installation to going through the tutorials, development, testing and implementation,” says Jay Kamradt, Assistant Manager, Information Systems at KMM.
The solution is saving over US$ 3,500 per day and we expect very quick ROI.
- The Challenge
- eKanban Efficiencies
- More Apps and More Savings
- Conclusion
- 2016 Update: Kawasaki converts iOS mobile apps to Android within hours
- Company and System Information
The Challenge
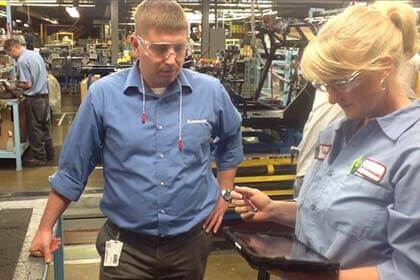
Kawasaki Motors Manufacturing Corp., U.S.A.’s consumer products division in Lincoln, Nebraska (referred to as KMM hereafter) manufactures All-Terrain Vehicles (ATV), Personal Watercrafts (Jet Ski®), Utility Vehicles (Mule™), Recreational Utility Vehicles (RUV – Teryx™) and wheels for ATVs and utility vehicles. These products are shipped throughout North America and exported to Japan, Europe, Australia, New Zealand and to other locations around the world.
KMM operates on a ‘just-in-time’ basis to eliminate expensive warehousing and over-ordering of parts. In this lean manufacturing environment, Kanban is used to signal the need to move parts from the warehouse to the production floor.
Traditionally Kanban is implemented using cards that are attached to a parts box. When a parts box at the assembly line becomes empty, the empty box and attached Kanban card are returned to the factory store. The factory store then replaces the empty parts box at the assembly line with a full box and contacts the supplier to replenish the amount of parts mentioned on the returned Kanban card. When the supplier’s order is delivered into the factory store, the Kanban card is attached to the box, completing the cycle. The process is meant to provide the exact amount of parts required, with just a small buffer of spares.
Up to recently KMM used the Kanban card system at its 4 assembly lines. KMM uses up to 4,500 Kanban cards per day and during each Kanban cycle, 8 to 10 people would handle a card. The labor costs for handling cards was estimated to be $3,000 per day.
There were other inefficiencies to the manual card system as well, according to Kamradt. “Cards could get lost, resulting in late delivery of parts. Also, there was no way of stopping staff from turning in Kanban cards early. Workers were sometimes hoarding 3 to 4 days of inventory at the assembly line, when they only needed a buffer of 4 hours.”
Kamradt explains, “We have been talking about eKanban and using mobile devices for other inventory and production related tasks since 2005. Other projects kept getting priority and it wasn’t till October 2011 that we got some key business users together and laid out what needed to be done. We have the in-house experience to customize our ERP Frameworks solution, but we didn’t think we had the skills to develop native mobile apps ourselves. The project was well underway when LANSA made its LongRange mobile development tool available and we were keen to get on the beta program in April 2012.”
We didn’t think we had the skills to develop native mobile apps ourselves.
eKanban Efficiencies
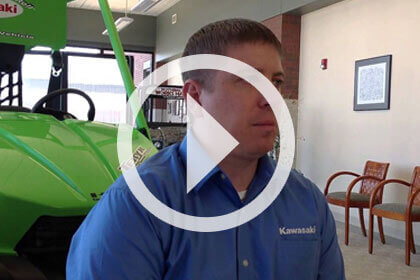
With some guidance of a professional services consultant from LANSA, KMM developed its first LongRange mobile app. The app allows the assembly inventory specialists, nick named parts-police, to scan-in or enter deliveries of parts at their assembly line and to monitor the balance of parts at their line and on the floor. When the assembly of a certain unit starts, e.g. an ATV, the ERP system is notified and it allocates the parts it needs for that unit. Since it is now recorded exactly which and how many parts are kept at each assembly line, the allocation will automatically trigger a pick transaction when the inventory of a part at an assembly line falls below a specified minimum.
Kamradt explains, “Previously once parts left the warehouse, we didn’t have any means to record where on the assembly floor they went or how many were accumulating there. Now we have an accurate real-time recording of parts anywhere on our premises, whether in the warehouse or on the assembly floor.”
“Having the mobile app allows for total accuracy. We now keep only 4-hours worth of parts on the floor and for bulk items even less. In addition to leaner inventory procedures, we now have a better and safer work environment. In the past the assembly lines could become a safety hazard cluttered with boxes and parts. The freed-up space also allows for more flexibility, opening up the possibility to produce additional models on an assembly line.”
“When we started the project we did an ROI analysis. We use up to 4,500 cards each day and 8 to 10 people would get involved in each kanban cycle. Based on the card being handled on a average 10 seconds each time and average wages being $30 per hour, we estimate to save $3,000 per day, or $747,000 per year, in labor costs directly related to staff not having to handle the manual kanban cards.”
KMM expects to save another $190 per day, or $47,500 per year, because there is no need any more for someone to walk around with a knife cutting a slit into each box and inserting a card. This saves 1000s of knife swipes a day. Now barcoded pick ticket labels are printed and affixed to the box. Other estimated savings include reduced labor for analyzing part shortages 5 hours per day and for running hot parts 16 hours per day, adding up together to more than $155,000 per year.
“We believe our ROI on eKanban is going to be very short, less than six months,” says Kamradt.
Having the mobile app allows for total accuracy and better quality control.
More Apps and More Savings
The LongRange tutorials together with their first working app as a best practice example, provided enough material for KMM’s IBM i developers to get themselves familiar with developing mobile apps. A team of 3 developers then developed 5 more apps. All the apps are native, touch enabled with dropdown lists, check boxes, buttons to start the scanner and so on. The apps were implemented at the first assembly line in early July, only 2 months after LongRange became available. The other 3 lines followed each other with one to 2 months in between.
An app for scrap reporting allows assembly supervisors to scan in scrap items. Previously the assembly line supervisor would compile a handwritten list at the end of the day of all the items that had ended up in the scrap bin. A carbon copy of that list would be sent to the quality control department where a clerk would spend most of her day rekeying the lists from all 4 assembly lines. The procedure was time consuming and riddled with all the usual inaccuracies associated with handwriting and rekeying.
“Now with the LongRange app, our parts-police at the assembly line scan scrap items throughout the day and, where needed, enter sufficient detailed comments. Automating the process using mobile technology saves our quality department a lot of time and makes the information that we track far more accurate,” says Kamradt.
An app for cycle counting allows a worker to adjust the inventory while on the floor and generate a pick ticket if needed. Another app allows workers to record the moving of inventory within the warehouse. Previously these inventory movements were simply not recorded, because there was no workstation on the floor. Workers would lose time trying to locate misplaced inventory, now the recording of inventory is far more accurate.
An app for online/offline reporting lets the assembly line supervisor scan when an assembled unit needs to be pulled of the line for repair, for example because there is something wrong with the engine of an ATV. “In the past those units would just sit next to the assembly line and we have no idea when it got there or how many times the same issue had come up. Now we are recording in real-time when units are coming off the line and the reasons why. This allows us to analyze the data and address the issue more timely, whether it is a parts problem with a supplier or a training issue with an assembly worker. The real-time recording allows for better quality control,” says Kamradt.
An app for engineering change notifications (ECNs) allows for the real-time recording of when a changed bill-of-materials comes into effect, e.g. the use of another radiator in an ATV. In the old system the change would be implemented on the assembly line and the VIN (Vehicle Identification Number) of the first unit with the new part would be recorded on a piece of paper, but in the ERP system the bill-of-material would not be changed till a specific job ran during the night. Other details needed to be backflushed to the VINs as well, which was not always precise.
“Now we have a app that informs the parts-police about ECNs that are coming up and they can activate the new bill-of-material through LongRange at the exact right moment. We now have an accurate recording of which parts are used in which units. If anything comes up from a quality standpoint, we know exactly which VINs are affected,” says Kamradt.
The mobile apps play a key role to record and track inventory on the assembly lines. But there is more involved in the eKanban solution. KMM used Visual LANSA to develop an application to record the ‘hanging’ of a unit at the assembly line. When a unit is hung the system creates a unit master record, a work order and prints documents for the unit. The system also allocates inventory and creates pick transactions for any parts the allocation drives below a dynamically created minimum value. Another application allows staff in the receiving department to view pick transactions that have been created by the assembly lines, print out pick labels, pick parts and deliver them to the assembly lines.
Users on the floor find the LongRange developed apps intuitive, reliable and stable.
Conclusion
Paul Kramer, Manager, Information Systems at KMM, explains “We used the LANSA version of the LongRange server, rather than the LongRange RPG version. Our developers come from all walks of life. Some have an RPG background, some are COBOL trained and others have Microsoft.NET skills. Using in-house skills, we initially thought our only choice was going to be mobile browser based apps, but that would have made it more difficult to use an external scanner and would also be less user friendly. Mobile access is only part of the eKanban puzzle, but it is a very visible and essential part. With LongRange we were able to handle the entire project ourselves, including mobile access.”
“Our developers found LongRange easy to learn and development was fast. We got our first series of apps out in just 2 months, including installing, going through the tutorials, development, testing and implementation,” continues Kamradt.
“As far as the users on the floor, their experience is that the LongRange developed apps are intuitive, reliable and stable. We haven’t had any issues or a need to revisit code. We developed the apps, they are in production and they have been running fine. The apps are now a crucial part of our new procedures and we cannot run the assembly plant without them.”
“We implemented LANSA’s ERP Frameworks solution in 2002 and since then we have dedicated a lot of IT resources to make things better for the office workers. The production area is where we make our money and we decided that it’s time to start improving their processes. What we have done today is just the beginning. We are going to keep improving the processes and roll out more mobile apps for the assembly floor and soon also for quality control and the receiving warehouse,” concludes Kamradt.
“My advice to other IBM i shops is to jump in with both feet to provide users with mobile apps. It won’t take you long to realize the benefits.”
We got our first series of apps out in just 2 months, including installing, going through the tutorials, development, testing and implementation.
2016 Update: Kawasaki converts iOS mobile apps to Android within hours
Normally a large undertaking, in 2016 KMM was able to convert its native LongRange iOS applications to Android without changing a single line of source code. “No development time was required,” said Kamradt. “We literally downloaded the LongRange app from Google Play, configured the Android devices to communicate with our IBM i and the handhelds were ready for production within a matter of hours.”
The iPad devices were performing well, but Kawasaki experienced battery life and Wi-Fi connection issues with the iPods, as well as the devices being susceptible to breakage on the warehouse floor. The iOS devices also required mobile device management solutions which incur additional fees. “These challenges, combined with LongRange’s support for the lower-cost Android platform, was the catalyst for change,” explained Kramer.
Kramer and his team began testing the Zebra TC70, an enterprise-class Android device built specifically to withstand the needs on shop floors. Porting the apps from iOS to Android was pain free because LongRange apps are managed from a single code base. In addition, since LongRange was already available in Google Play, KMM was able to get the app into production without having to wait for the normal approval process.
Today KMM still operates iPads on the assembly line, but the devices are nearing the end of their life. Now that LongRange has extended its support to the Windows platform, KMM is looking to investigate moving to Windows Surface devices.
Company and System Information
- Kawasaki Motors Manufacturing Corp., U.S.A. manufactures and distributes small engines, ATVs, personal watercraft, Mule and Teryx utility vehicles and passenger railcars from its manufacturing plants in Maryville, Missouri and Lincoln, Nebraska.
- The mobile devices used by KMM’s assembly staff are iPads with a Bluetooth Socket 7P scanner attached.
- KMM’s Lincoln plant has been running LANSA’s ERP Frameworks since 2002.
- KMM’s IT department in Lincoln consists of 11 staff, including infrastructure support.
- For more information visit:www.kawasaki.com
Related Links