ROBINSON MANUFACTURING’S NEW ERP SYSTEM OFFERS A ONE-STOP SHOP
Robinson Manufacturing Company, based in Dayton, Tennessee in the US, is a supplier of basic and fashion boxer underwear, loungewear and activewear to both the retail and wholesale markets. Robinson uses Visual LANSA to redevelop its core applications and also to offer a web portal to its vendors where they can securely manipulate data, create shipments and print case labels.
Fred Coulter, Director of IT at Robinson, says, “Users now have a far more productive work environment. They have access to more information and the information is better organized. We are very customer focused and do our best to provide what the customer wants. LANSA provides a practical and flexible development environment in which we can meet customer and user requests.”
Users now have a far more productive work environment.
- From UNIX to IBM i
- Rich-client Windows and Web
- Flexibility and Control
- The Importance of Proper System Design
- 2010 Update: Integration
- Company and System Information
From UNIX to IBM i
Robinson Manufacturing was established in 1927 as an apparel manufacturer, starting with men’s boxer shorts. The 60s, 70s and 80s were times of tremendous growth and resulted in the addition of several product lines. Robinson Apparel® and Boxxerz® have become leading brands in the imprinted sportswear market, however the majority of the company’s products are private label. Customers include major retailers and big-name sportswear and leisurewear brands.
Robinson’s corporate and sales offices, distribution centers, manufacturing and cutting plants are based in Tennessee, with one subsidiary, College Concepts, being based in Atlanta. Today the company imports as many products as it manufactures, so smooth communication with suppliers has become a top priority.
Robinson’s in-house developed ERP system, UNIX based and developed in FilePro, has been around for nearly two decades and was due for replacement, explains Coulter. “It was inflexible and hard to navigate for end users. Maintenance and user support were time consuming and the system had become patchy over time. It wasn’t suitable to extend to the web for access by vendors, which was a high priority item on our agenda.”
When Robinson implemented a Pick Ticket and Warehouse Management System in the late nineties (PkMS from Manhattan Associates), it happened to be running on the AS/400. The platform performed well and it made sense to move the company’s ERP system to the same platform. Robinson investigated several packaged ERP solutions and even trialed one, but couldn’t find a solution that was a close enough fit.
“We would have had to make a massive amount of modifications to make a packaged solution suitable for the way we run our business,” explains Mark Whitt, Programming Supervisor. “Very few solutions can handle our multi-company multi-division business model, industry specifics like color and size and manage our import and manufacturing equally well. But most importantly, with a packaged solution we would never have the flexibility and control that comes with having an in-house developed solution.”
The plans for a packaged ERP solution were abandoned and Robinson started investigating development tools instead. “Developing in RPG was out of the question,” says Whitt. “We decided on LANSA because of its productivity and ability to run on multiple platforms. LANSA’s web capability was also far ahead of other tools and we saw immediately how we could put that to use.”
We decided on LANSA because of its productivity and ability to run on multiple platforms.
Rich-client Windows and Web
Robinson’s first two LANSA developed modules consisted of a Work Order system and a Plant Management system.
Next came Robinson’s first web application, the Vendor Shipment Management System (VSMS). The VSMS provides suppliers with real-time access to purchase orders and lets them create and maintain shipments, shipping dates and cases. They can also print the shipping manifests and bar-coded case labels. Upon closing a shipment, the VSMS creates an Advance Shipment Notification in Robinson’s ERP and PkMS systems. The VSMS has recently been extended with a quality-auditing module, allowing quality control staff to quickly locate and test the goods as soon as the shipment arrives.
“The VSMS gives complete visibility of vendor shipments right across our organization and provides all the necessary information for receiving them in our warehouse,” explains Whitt. “We know exactly what’s on its way to us, when we can expect to receive it and how goods are packed.”
Other LANSA-developed applications include Report Management, Time-and-Attendance, Finished Goods and a Garments Specification system.
Important master files have history time stamps, triggered by field level changes, keeping a log of changes made to a record. Most of Robinson’s forms have a history-button built-in, making a record’s modification log available to end users. It answers a lot of questions that would otherwise have to be dealt with by the IT team.
All reports are developed in-house with LANSA, mostly in PDF format because of images that are embedded. Users can also export data to Microsoft Excel. Robinson uses its own deployment solution, which is managed through a LANSA-based menu application.
“We are a big user of LANSA’s Repository for centrally defining triggers and business rules and also rely on its impact analysis and controlled check-in and check-out facilities to make managing group development easy,” says Whitt.
Robinson uses Visual LANSA for all new development and chose a rich-client Windows interface for internal users and a web interface for vendors and other third party users. Being new to both the IBM i and to LANSA, the learning curve was initially steep, admits Whitt. To ease the learning process, the first two modules were developed with help of LANSA partner TssiGlobal, from Kentucky.
The Order Entry and Billing applications still run on the UNIX system, necessitating bi-directional data exchanges between the UNIX and IBM i systems to keep the data in synch. Master file data is maintained on the IBM i and exchanged instantly on updating a record, while transactional data is refreshed with 10-minute intervals. Whitt aims to redevelop these last two remaining applications in the coming couple of months and provide web access to customers as well.
LANSA’s Repository facilities make managing group development easy.
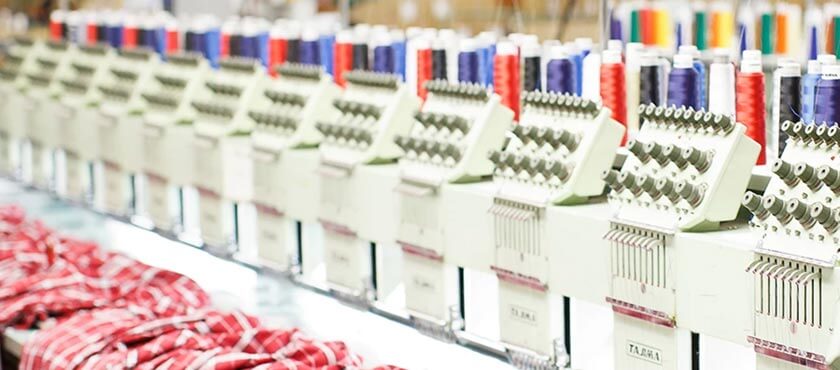
Flexibility and Control
Kathy Griffin, Director of research and development, comments that even though the Garment Specification System (GSS) has only recently been launched, the apparel design team already experiences the benefits. “The data management & collaboration tools in the GSS enable us to better communicate internally and to be more integrated with sourcing, manufacturing and external partners.”
“Being able to link from product specification to quality assurance records & product history, provides us with better visibility of potential product issues, allowing us to take corrective action at an earlier stage of the manufacturing process. The system frees the designers to focus on creative and technical product development and helps us to take a product seamlessly from style conception through product commercialization,” says Griffin.
“The biggest benefit from the users’ standpoint is they have a one-stop shop for all the information they need,” Whitt explains. “They can drill down into detailed information without having to start separate programs. Also, nearly all the applications allow users to export data in an organized way into Microsoft Excel or Word. We wrote the applications in a flexible way, so that users can filter data in as many ways as they want. Once the data is in Excel, they can produce their own sub-reports and analyze the data without assistance from IT.”
“It’s a huge benefit for us to be able to securely provide data and let users manipulate it the way they see fit, instead of them having to wait for IT to develop an application,” says Whitt. “Even for the users who are not so PC knowledgeable, the filter programs make it easy to get exactly the data they want into Excel and formatted in the right way.”
Users now have a far more productive work environment, according to Coulter. “They have access to more information and the information is better organized. We took the time to analyze and rearrange information and design the system in a flexible way that is custom fit for our organization.”
“We are very customer focused and do our best to provide what the customer wants. For that we need a productive and flexible development environment and to be in control of our own solution.” Coulter illustrates the benefits of this with a recent example, where Robinson made a special arrangement for a major customer to accommodate a change in the way their inventory is handled and at which point ownership is transferred. “It was a dramatic change in the way we do business with just this one customer, which affected ordering, billing and shipping. Using LANSA and our own IT team we were able to deliver that change in just a few weeks.”
The filter programs make it easy to get exactly the data you want into Excel.
The Importance of Proper System Design
Whitt and Coulter both point out that initial development took longer than planned, as they spent a lot of time and consideration on proper system design, creating common ancestor forms, building reusable components and becoming familiar with the GUI and the event-driven development paradigm.
“One of the reasons we selected LANSA initially was its productivity, but the quality of the applications we create with it is now more important. When you do things right the first time, you only have to do them once. We hardly ever have to revisit code already written,” concludes Whitt. “Using LANSA’s reusable components, there’s no redundant programming that you have to do over and over again. Also, the availability of components increases over time, making the development cycle faster for the more recent projects.”
“The time you spend upfront is gained back later, so it’s worth the effort,” concludes Coulter. “The biggest time saving comes from the ease of supporting the new application. In the legacy system we found ourselves much of the time helping users with data extracts, researching system issues and answering questions that users should be able to deal with themselves. We have taken ourselves out of that loop and made it easy for our users to deal with the information on their own.”
Using LANSA’s reusable components, there’s no redundant programming.
2010 Update: Integration
Since the above case study was written, Robinson has extended its use of LANSA technology to include LANSA Composer, a design and execution platform for integrating business activities involving transport, data transformation and custom business processing. Robinson uses Composer for numerous projects, including:
- UPS address validation, where Composer validates the address and classification with UPS via a SOAP HTTP/XML Request and Response
- Moving inbound EDI Purchase Orders from Gentran to the ERP system
- Processing web visit logs into a database for reporting
- Processing logs regarding PC backups and email alerting users with missed/failed backups
- Converting spool files to CSV and PDF formats
- Report Distribution that includes scheduling, creating, printing and emailing of reports
- Converting SQL files to CSV for one-time report requests by Excel users
Company and System Information
- Robinson manufactures and markets underwear, loungewear and active wear in private label and under the Robinson Apparel® and Boxxerz® brands. The company’ s facilities in South Dayton, TN, consist of 120,000 square feet of floor space, housing its corporate and sales offices as well as one of its manufacturing facilities. Just across town are two distribution centers and a cutting facility, totaling 200,000 square feet.
- Robinson uses two IBM i systems, one for its PkMS Warehouse Management System and one for its ERP system.
- Out of a development team of six full time developers, three are developing the new LANSA system and three are maintaining the old FilePro system.
- For more information visit www.robinsonmfg.com